Optimalizace čalounické výroby ve společnosti BorcadTrénink na pracovišti
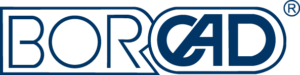
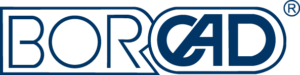
Oblast řešení
Optimalizace výroby
Náš úkol
- Snížení výrobnách časů o 30%
- Snížení počtu obsazených paletových míst v prostoru čalounické výroby o 50%
- Zvýšení produktivního času předáka dílny z 25% na 70%
- Definice maximální kapacity výroby
Průběh
Cílem půlročního projektu ve společnosti Borcad, která se primárně zabývá výrobou sedadel pro kolejovou techniku bylo nastavit a optimalizovat novou čalounickou výrobu. Do roku 2017 probíhala veškerá výroba čalounění v kooperaci.
Náš projekt startoval v září 2017 a navazoval na interní projekt, jehož cílem bylo zavedení výroby čalounění. Šití a kompletace čalounění bylo zahájeno prvními sériemi koncem již srpna. Vše bylo ovšem na počátku jak z hlediska počtu vyrobených kusů, tak nastavených časů a procesů. Nedostatečný byl také návoz materiálu, návaznost operací, tok materiálu mezi pracovišti, nevyužívaly se víceméně žádné přípravky, výroba se již od začátku dostávala do skluzu.
Po vstupní analýze jsme spolu s vedením společnosti Borcad definovali konkrétní cíle projektu a to na zkrácení výrobních časů o 30%, snížení počtu obsazených paletových míst v prostoru čalounické výroby o 50%, zvýšení produktivního času předáka dílny z 25% na 70% a nadefinovat maximální kapacitu výroby s návrhem dalších investic. To vše s termínem 28.2.2018.
Nejprve bylo potřeba definovat současnou výrobní kapacitu, vypočítat potenciální důsledky nedostatečného množství lidí a poté pomocí Spaghetti diagramu „rozpitvat“ tok materiálu a pohyb pracovníků. Následně jsme vytvořili nový koncept materiálového toku s využitím přepravních vozíků, a to již při samotném vychystávání a návozu materiálu ze skladu. Sedadlo se skládá z mnoha menších či větších dílů a systém uložení jednotlivých částí hraje při prvních výrobních krocích klíčovou roli. Tří až pěti patrové vozíky s přesně nadefinovaným způsobem uložení byly trefou do černého.
Na základě Spaghetti diagramu, sledování „cvrkotu“ při běžném chodu a potřebě snížit množství obsazeného paletového prostoru jsme navrhli a zrealizovali nové rozmístění jednotlivých pracovišť s ohledem na co nejkratší trasy a návaznost operací a minimum rozpracované výroby. Výroba čalounění má několik „prvních“ operací, a proto bylo důležité najím body střetu jednotlivých komponentů a sestav.
Další důležitou součástí celého procesu je příprava výroby. Stříhání pásků, suchých zipů a spousty dalších dílů jsme se snažili maximálně automatizovat, což se podařilo.
Nízký počet lidí a využívání jejich schopností na pravém místě byl dalším problémem. Pracovnice, které umějí šít nemohou být využívány pro pomocné operace. Například pro navlékání čalounění, což je velice fyzicky náročná operace, jsme okamžitě začali hledat silový typ pracovníků, kterým nevadí stereotypní práce.
Skluz ve výrobě, který vznikal od počátku projektu a na jeho konci proměnil v třítýdenní předstih a možnost předvyrobit si dostatečné množství sad.
Výsledek
Bylo dosaženo snížení výrobních časů o 28,3%, počet využitých paletových míst se snížil o 66%, jediné, produktivní čas předáka se zvýšil na 45%. Pro maximální kapacitu dílny jsme využili Citlivostní analýzu.
Máte zájem o spolupráci?
Chyba: Kontaktní formulář nebyl nalezen.